These tools are used in the industry for precision grinding but also for rough processing in the foundry and steel industries.
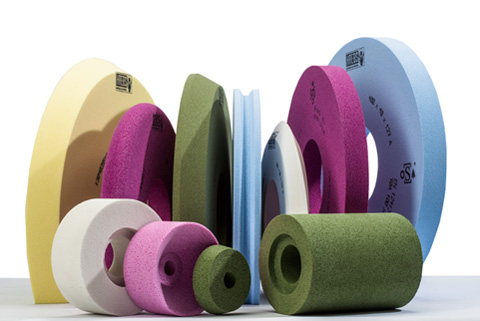
These wheels still prevail in the application of precision grinding.
Grinding wheels in vitrified bond
These wheels still prevail in the application of precision grinding. The main advantage of grinders in vitrified bond is the possibility to control the porosity of the structure of the grinding wheel. These tools combine what is considered impossible: with a minimum content of the bond the amount of the grinding grain is maximised in high porosity. The result is a tool with excellent features in grinding special steel structures.
Grinding wheels in vitrified bond are fired at temperatures up to 1300°C. The vitrified bond and with that also grinding wheels are resistant to chemical reactions and ageing. Their expiry date is unlimited. However, the nature of the bond makes these grinding wheels sensitive to blows and sudden changes in either temperature or pressure.
These wheels still prevail in the application of precision grinding. The main advantage of grinders in vitrified bond is the possibility to control the porosity of the structure of the grinding wheel. These tools combine what is considered impossible: with a minimum content of the bond the amount of the grinding grain is maximised in high porosity. The result is a tool with excellent features in grinding special steel structures.
Grinding wheels in vitrified bond are fired at temperatures up to 1300°C. The vitrified bond and with that also grinding wheels are resistant to chemical reactions and ageing. Their expiry date is unlimited. However, the nature of the bond makes these grinding wheels sensitive to blows and sudden changes in either temperature or pressure.
This grinding is the most frequently used grinding in the industry. The wide range of grinder components includes fine injector needles for injection technology through gear shafts to extremely heavy rolls for the paper industry.
Besides the well-established standard grinding wheels, the vitrified bonded CBN and diamond grinding wheels are increasingly being used in the industry.
The traditional round grinding includes processes as are:
- OD round plunge grinding,
- OD round oscillating grinding,
- OD round angular plunge grinding,
- and inside diameter (ID) plunge and oscillating grinding.
There is also large scale grinding on centerless machines where the grinding is through-feed and plunge-feed.
Non-round grinding – for example, of camshafts, pump rings or pressing tools – is one of the most complex grinding applications. The non-round contour leads to changing contact and movement conditions in the contact zone.
The properties of the grinding tool must be appropriately matched to the process. Based on years of experience, KREBS & RIEDEL can provide highly efficient solutions.
In this grinding operation, surfaces are flattened in parallel with the periphery of the grinding wheel or its face. A number of process variations exist. These differ mainly in the position of the axis of the grinding wheel to the workpiece surface.
Most typical workpieces are punching and blanking dies, guide tracks on machine beds, various knives, etc. Certain tools demand complex profiles where grinding is done with pre-profiled grinding wheels.
The most widely used operations in surface grinding are reciprocating surface grinding, profile grinding and face grinding.
Gears are among the most important mechanical elements in transmission systems of vehicles and machines. The demands of these products with respect to power transmission or smooth running are continuously increasing.
This is why gear grinding represents one of the crucial grinding processes in ensuring a high-quality ground surface.
The most frequently used techniques of gear grinding are profile grinding, continuous generative grinding, and bevel gear grinding.
Crankshaft grinding is very specific and demands a lot from tools. Besides vitrified grinding wheels, this type of grinding makes use of CBN grinding wheels as well. For different strategies of grinding adapted specifications of grinding tools are necessary.
The machining of the flange and pin is usually performed with an angular infeed grinding process. Here conventional grinding wheels in aluminium oxide or CBN grinding wheels with vitrified bond are used.
The synthetic resin bond consists of phenolic resin and a number of fillers which influence the features of the bond and consequently of the grinding wheel.
Grinding wheels in synthetic resin bond
The synthetic resin bond consists of phenolic resin and a number of fillers which influence the features of the bond and consequently of the grinding wheel. Bonds ensure the elasticity of the grinding wheel and the binding of the abrasive grains.
Synthetic resin bond hardens at temperatures from 170 to 200°C. In contrast with grinding wheels with vitrified bond, grinding wheels with synthetic resin bond are not as sensitive to changes in temperature and better withstand blows and pressure. On the other hand, this bond can only be stored for a limited period of time and is sensitive to chemicals.
Grinding wheels in synthetic resin bond are used for achieving high rates in material removal on rough workpieces and producing fine surface finishes.
Rough grinding wheels are applicable at very high cutting speeds and in high performance rough grinding. Wheels come with or without a reinforced design with glass fibres. The use of such wheels is suitable for foundries and steelworks in grinding or cleaning surfaces.
Grinding wheels in synthetic resin bond can also be applied in the processes of circular precision grinding, surface grinding and in sharpening tools.
shapes of grinding wheel sides
Standard grinding wheel shapes
Shape 1
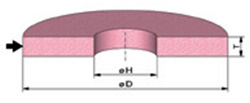
Shape 2
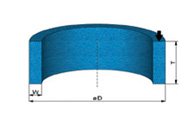
Shape 3
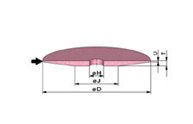
Shape 1, shapes of grinding wheel sides
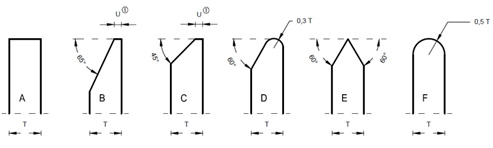
Shape 4
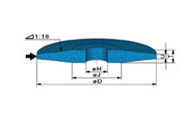
Shape 5
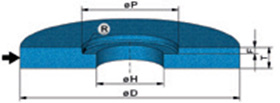
Shape 6
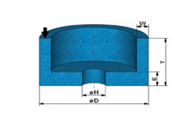
Shape 7
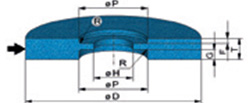
Shape 11
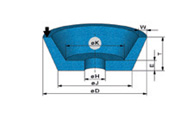
Shape 12
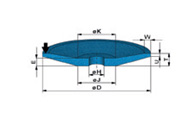
Shape 20
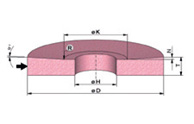
Shape 21
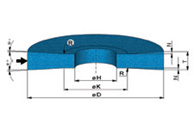
Shape 22
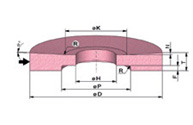
Shape 23
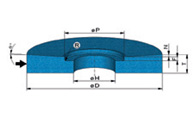
Shape 24
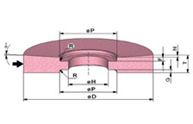
Shape 25
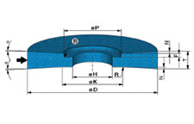
Shape 26
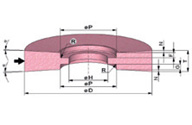
Shape 38
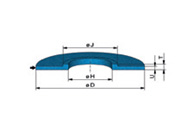
Shape 39
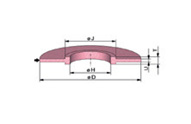
Company
Brusilna tehnika d.o.o.
Masljeva ulica 3
1230 DOMŽALE
Slovenia
Phone.: +386 1 7291265
eMail: info@brusilnatehnika.si